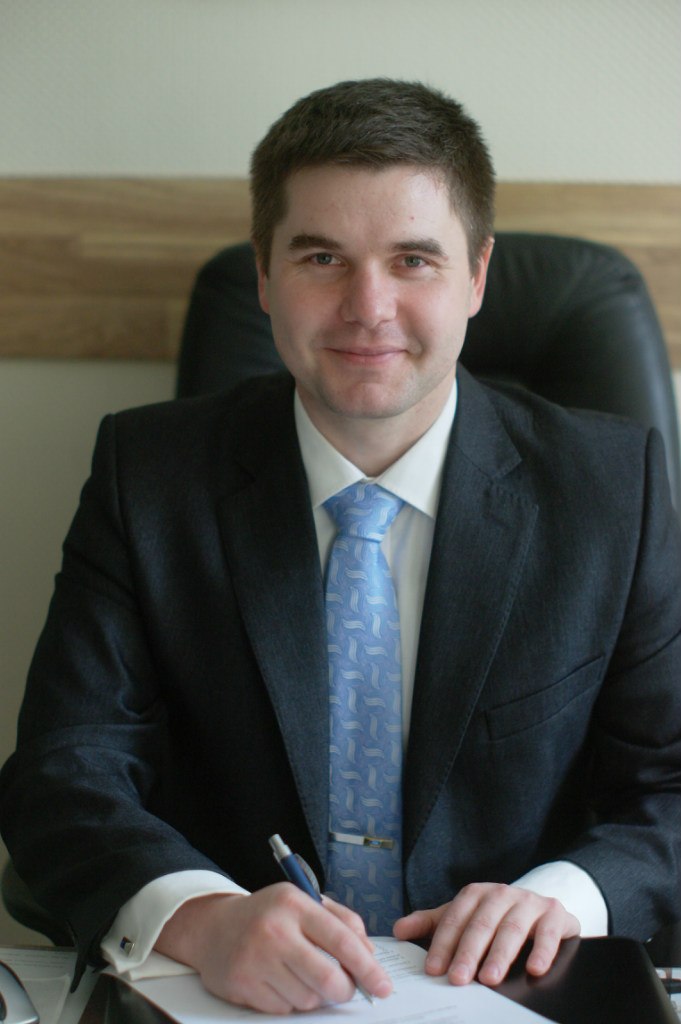
- Виталий Геннадиевич, как проходила работа по изготовлению деталей?
- Мы взяли за основу схему и 3D-модели деталей малоразмерного двигателя разработанную на факультете ДЛА. Для первоначальных испытаний были выбраны самые ответственные детали - камера сгорания и турбина. С использованием программного обеспечения были заданы режимы сплавления и виды поддержек. На изготовление каждой детали ушло около 10 часов. Камера сгорания и турбина изготовлены из металла, и после стендовых испытаний они могут использоваться в реальном двигателе. Сразу оговоримся, пока наши «выращенные» детали – образцы, которые необходимы для корректировки конструкции самого двигателя для получения более точных эксплуатационных параметров.
- Чем аддитивные технологии отличаются от традиционных?
- Раньше на предприятиях, чтобы изготовить деталь, использовали традиционные технологии, для которых требовалась оснастка. Что всегда было связано с дополнительными временными затратами. При этом производственный цикл мог достигать от трех до шести месяцев. Сегодня при аддитивном производстве затрачивается порядка 48 часов.
Новые технологии позволяют использовать практически ровно то количество материала (металлического порошка), которое необходимо для готовой детали. Кроме того, сокращается время на создание прототипа детали и самой модели двигателя. В совокупности это даёт ощутимый экономический эффект: снижаются трудозатраты при производстве высокотехнологичной продукции, объём материала и время обработки.
И ещё одно важное отличие – возможность быстро менять форму продукции и ускоренное получение деталей. Ведь современное производство характеризуется относительно быстрой сменой продуктов. При этом зачастую меняются не основные компоненты, определяющие функциональное качество продукта, а дизайн - корпусные элементы, элементы декора и так далее. По этой причине в ряде случаев отпадает необходимость в дорогостоящей инструментальной оснастке. Благодаря АМ-технологиям можно сделать матрицу или пресс-форму из лёгкого сплава с меньшим ресурсом. Пресс-форма может быть сделана вместе с каналами охлаждения произвольной конфигурации, что невозможно сделать при обычных методах механообработки.
- По составу металла и качественным характеристикам «выращенные» детали уступают обычным?
- В наших деталях используется металлические порошки, которые имеют тот же химический состав что и заготовки для традиционных методов обработки. Однако результаты прочностных свойств полученные на образцах соизмеримы с заготовками полученными литьем и уступают пока штампованным. Существует другая проблема – производство отечественных металлических порошков. Сегодня в России в ФГУП «ВИАМ» ведутся разработки порошковых отечественных материалов для установок селективного лазерного сплавления, не уступающих по качеству зарубежным аналогам. В частности, в отечественном производстве уже применяются российские металлические порошки жаропрочного сплава на основе никеля.
- Но ведь к изделиям аэрокосмической отрасли предъявляются более высокие требования?
- Несомненно, изделия аэрокосмической техники являются высоконагруженными изделиями, они сложны как в конструктивном, так и в технологическом исполнении. Условия, в которых работают детали, достаточно жесткие, следовательно, и требования к качеству изготовления таких деталей предъявляют высокие. Стоит отметить, что проведенные исследования на образцах, полученных на нашей 3D машине, полностью удовлетворяют требованиям, предъявляемым к изделиям аэрокосмической техники. Выращенные образцы показали хорошие результаты при высокой температурной нагруженности, также были получены положительные результаты при прочностных испытаниях. Все это свидетельствует о том, что качество получаемых изделий достаточно высокое, и, несомненно, они найдут свое применение в аэрокосмической отрасли.
- Какие перспективные направления в области аддитивных технологий разрабатываются сегодня в СГАУ?
- К основным направлениям относятся разработка и исследование процесса селективного лазерного спекания изделий из композиционных материалов, а также разработка 3D установки, позволяющая изготавливать сложнопрофильные элементы авиационных двигателей методом прямого лазерного выращивания. Решение данной задачи позволит в короткие сроки получать физические прототипы новой техники и осваивать серийное производство. Это особенно актуально с учётом стратегии импортозамещения и импортоопережения в высокотехнологичных отраслях. Это напрямую относится к газотурбинному двигателестроению. Так в рамках Федеральной целевой программы «Исследования и разработки по приоритетным направлениям развития научно-технологического комплекса России на 2014 – 2020 годы» мы выступаем соисполнителями в разработке первого отечественного трехмерного высокопроизводительного принтера для печати из металла. Все разработки ведутся совместно с Санкт-Петербургским политехническим университетом. Первым пользователем нового принтера станет ОАО «Кузнецов», для которого в 2017 году в рамках данного проекта необходимо изготовить образец установки.
Беседовал Дмитрий Попов